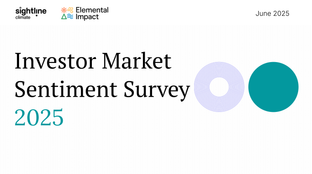
🌎 Our 2025 climate tech investor pulse check
Survey results: what’s working, what’s stalled, and what’s missing
Unpacking the bio hype from plastics’ feedstock to end of life with Hannah Friedman and Keeton Ross
Turns out, there wasn’t a great future in plastics. As the all too ubiquitous container of our society, plastic shapes how we eat, what we wear, and quite literally forms our bags, boxes, homes, cars, and most things in between (e.g. fish).
Our prior penchant for plastic has driven a burgeoning petrochemical industry that sucks up 14% of global oil use as the feedstock. Within the last two decades, global plastics production has doubled to 460M tonnes and jumped to ~3% global GHG emissions to meet our insatiable demand.
The real dirty wrinkle with plastics cuts deeper, past production emissions into mismanagement at the end of life. The damning figure is our global recycling rate, which has decreased from ~9% to just over 5%, accompanied by headlines on the epic failures / need to expand composting infrastructure and overflowing landfills that recently ignited during heat waves. Though, there’s a glimmer of hope for a new lease on plastics’ end of life. India and other countries have announced bans on some formats of single-use plastics, and California went one step further requiring all packaging to be recyclable or compostable by 2032. In funding, we’ve tracked $1.6B of venture capital deployed towards biobased packaging and chemicals innovators since 2020, alongside a recent spike in M&A activity for composting (e.g., Generate Capital acquiring Atlas Organics).Framing plastics’ emission scope can get quite nuanced depending on where you draw the LCA line.
There are three major levers to plastic decarbonization:
1) Raw materials e.g. feedstock
2) Manufacturing e.g. process energy
3) End of Life e.g. recycling, composting, landfill
With the sweeping caveat that reduce, reuse, recycle always reigns true, bioplastics have entered the plastic decarbonization ring pulling on 2 out of the 3 decarbonization levers: using a 1) biobased feedstock and/ or being 2) biodegradable at end of life (more on this later). But bioplastics are hardly a shoo-in; the “bioplastics” space is rife with misnomers and confusion.
In this issue, we go plastic (it’s fantastic!) – where it costs us, where it’s changing, and how bioplastics are shaping some new reality. We’ll get to all that, along with genuine circular economy innovations, but first, let’s start with the basics.
A plastic is a polymer (poly meaning many) made up of a repeating chain of monomers (mono meaning one). Chain together multiple monomers and you get a polymer - voila, plastic! Plastics vary in weight, color, melting points, density, and barrier properties (like permeability to oxygen or moisture), among other things. These properties depend on which monomers are used, their chemical structure, order of assembly, and presence of any other chemicals such as additives. Think of plastics as one complex recipe - you can get fluffier muffins with different ingredients.
Generally, plastics fall under two general buckets: thermoset (durable and retain their form under heat) and thermoplastic (soften and melt under heat). The thermoset and thermoplastic lines break out even further by their resins, conveniently numbered 1 through 7:
1: PET (polyethylene terephthalate) - food packaging, single-use bottles, polyester
2: HDPE (high density polyethylene) - milk cartons, detergent bottles
3: PVC (polyvinyl chloride) - plumbing pipes, credit cards, medical tubing
4: LDPE (low density polyethylene) - garbage bags, plastic wraps, grocery bags
5: PP (polypropylene) - straws, prescription bottles, packaging tape
6: PS (polystyrene/ styrofoam) - takeout food containers, product packaging
7: Everything else! - a super ambiguous catch all
Not full on alphabet soup yet? The various monomers that add up to create polymers are also often referred to by their acronyms. MEG (monoethylene glycol) + TPA (terephthalic acid) = PET. But that’s (almost) enough chemistry for today. Most important to recognize is that depending on their properties, certain plastics may be more recyclable than others. PET (#1), HDPE (#2) and increasingly PP (#5) are the most recyclable of these traditional plastics, which is a good thing given their relative abundance in the market.
How do liquified dinosaur fossils resurrect as your Poland Spring bottle? Breaking down the plastics value chain is a bit of a Pandora’s box, so we’ve simplified it here (in yellow):
Conventional fossil-based plastics generally follow the path of:
Remarkably, this conventional fossil-based plastics value chain translates largely identically for the bioplastics value chain, as represented in blue. Now keep this value chain framework in mind as we get down in the *weeds* of bioplastics!
Bioplastic can mean that a material is biobased. Bioplastic can also mean that a material is biodegradable. These terms are not mutually exclusive; biobased refers to feedstock whereas biodegradable refers to the end of life of the material. Therefore, a petroleum-based plastic that is biodegradable counts as a bioplastic (e.g., PBAT), as does the vice versa of a biobased plastic that is not biodegradable.
As we’re ever eager to put the world into a 2x2, the complete universe of bioplastics comprises 3 of 4 quadrants - materials that are biobased and / or biodegradable. The lower left quadrant of conventional, fossil fuel-based plastics are excluded from the bioplastics definition (le duh) though most are recyclable.
The majority of frontier bioplastic innovators bridge the intersection of biobased and biodegradable, doing double duty to push the envelope of bio-benefits.
✅ Biobased feedstocks, ❌ Non-biodegradable
Materials: Bio-PET, Bio-PE, Bio #1-6
Companies: Resource Chemical (producing biobased FDCA), Virent*, Origin Materials*
✅ Biobased feedstocks, ✅ Biodegradable
Materials: Chitin, PHA, PLA, PEF (if MEG is renewable)
Examples: Genecis (producing PHAs from biogas of AD), Bloom Biorenewables (lignin-based biopolymers), Erthos (novel biopolymer from ag wastes), Mango Materials (producing PHAs from landfill methane), RWDC (producing PHAs), Shellworks (bacteria-produced “fat-like substance” to create rigid bioplastic and other chitin-based biopolymers for dissolvable films), FullCycle Bioplastics (producing PHAs from food waste), Cruz Foam (styrofoam-like bioplastic from shrimp shells), Plantic*, Total/ Corbion*, Futerro*, NatureWorks*, Danimer Scientific*, Origin Materials*
❌ Petroleum-based feedstocks, ✅ Biodegradable
Materials: PCL, PBAT, PBS
Examples: TIPA (⅔ biobased and compostable flexible films), PTT MCC Biochem* (producing PBS), Better Packaging Co (utilizes PBAT among other mixed biopolymers in compostable flexible films), Kintra Fibers (producing PBS-like material)
❌ Petroleum-based feedstocks, ❌ Non-biodegradable
Materials: Conventional plastics #1-6 (PET, HDPE)
Examples: Dow Chemical*, LyondellBasell*, Exxon Mobil*, SABIC*, ENI*
*Denotes public, JV, or acquired companies
The big buckets of biobased feedstocks are sugar, starches, fats and oils, woody biomass, and other organic waste (such as food diverted from landfills). For the former, there are sources of both virgin feedstock (e.g., trees and rows of corn grown specifically to produce bioplastics) and waste feedstock (e.g., rice husks or leftover corn stover after harvesting). Each biobased feedstock fundamentally varies in scalability, cost, market maturity, geographic distribution of availability, expected life cycle analysis impact, and ease of useability in downstream processes.
How do you take these biobased feedstocks and convert them into useful materials, whether as traditional recyclable plastics or compostable biobased plastics? Predominantly, these conversion pathways are chemical (e.g., synthesis, polymerization) and biological (e.g., fermentation). Then, taking material inputs to a finished packaging product generally follows the same value chain post-polymer.
Now that we’ve got biobased feedstocks on lock, let’s unpack the biodegradability’s own set of bioplastic caveats:
In other words, compostable is a subset of biodegradable. All compostable materials are biodegradable but not all biodegradable materials are compostable.
Any bioplastic that fits within the compostable sphere must meet a stringent and higher environmental bar. Certified industrially compostable materials must meet 4 requirements:
Despite biodegradability’s benefits, biodegradable materials will not necessarily biodegrade of their own accord in unmanaged environments such as landfills. Microbes are hungriest when necessary conditions on temperature, moisture, and oxygenation levels are met. If not, biodegradable materials can actually persist in the environment for long periods of time or worse, disintegrate into smaller and smaller microplastics invisible to the human eye. For this and a host of other environmental and human health reasons, no plastic or packaging should end up in landfills or our rivers and oceans. Instead, materials should be circulated optimally in controlled conditions by either being recyclable or compostable. This is exactly why entire states (e.g., California) are mandating their entire packaging portfolios be either recyclable or compostable by 2030.
In the upper left quadrant of our definitional 2x2, the biobased but chemically identical plastics (e.g., bio-PET) can be recycled alongside existing virgin (fossil fuel-based) plastics.
As consumers lean green, the market has responded with an outsized proliferation of new bioplastic materials, each with their own combination of feedstocks and processing requirements. But new materials don't necessarily solve plastic’s dirty challenges without considering the restrictions of the entire system of recycling and compost facility partners. Said bluntly, biodegradable is moot if the material isn’t managed under the right end of life conditions.
We’ve been confused by the labeling on many a recent water bottle made from new “recyclable biodegradable” bioplastics. Natureworks’ PLA brand Ingeo and PEF (yes, with an “F”?) being prime examples. PEF is a PET look-a-like, but with similar - and in some cases, better - physical performance properties like barriers. Avantium, who produces PEF, claims that their “plant plastic would decompose in one year using a composter, and a few years longer if left in normal outdoor conditions. But ideally, it should be recycled.”
Your spidey senses should be tingling. There’s a few things off here. First, composting is defined by the specific timelines of the process: certified compostable material needs to convert 90% of the organic carbon in a package to carbon dioxide within 180 days - not the year-long timeline cited. Second, decomposing over a few years if “left in normal outdoor conditions” frankly sounds a lot like littering, and early reporting on the material indicates that PEF is not biodegradable. Cue a host of lawsuits and concern that new bioplastics’ misuse of the term “biodegradable” could be more of a marketing ploy than physical reality. Seriously, a number of states have outlawed the term biodegradable in on-package labeling.
The reason that PEF, like many new materials, are not widely recycled despite being technically recyclable has less to do with the push of new chemistries and more to do with the pull (or lack thereof) from the economics of recyclers and composters. Three key factors determine the price of recyclers’ and composters’ end products. (Remember: these are commodity businesses that sell bales of recycled material and pounds of compost.)
First, cost. The petrochemical industry has optimized the ingestion of fossil-based feedstocks cheaply over centuries, and starting over with net new biobased feedstocks and biodegradable processes that are better and cheaper out of the gates is no easy feat. Consider cost across the lifecycle:
Feedstock: Varies by type (sugar, wood, agriculture residues, even human waste!) and volume, though feedstocks are generally the largest contributor to cost - and also differentiate price to the greatest degree
Opex: Varies a lot by process and feedstock types, particularly for bioplastics
Capex: Generally decreases with scale, but takes (expensive) time and infrastructure dollars
Second, scale limitations via technology scaling and feedstock scaling. Particularly for biobased plastics, the lab → pilot → demonstration → commercial scale-up challenges are particularly, well, challenging given constraints to sourcing massive quantities of waste biomass. Biomass is a hot commodity with competing existing demand from fuels and even carbon removal. A large amount of US corn and Brazilian sugar goes to biofuel production. Biobased feedstocks are therefore at the whim of commodity prices and system-wide land use decisions.
Third, convincing stakeholders. Most everybody hates change, including industrial partners who are skeptical of novel bioplastic innovations. This leads to a few key hurdles that innovators need to overcome:
After satisfying cost, scalability, and performance, new materials innovators must convince and cajole a bevy of stakeholders throughout the relatively old-school plastics value chain that’s rife with centralized infrastructure and industrial incumbents. Regardless of innovators’ potential, momentum favors the incumbents and it can take an entire decade, if not longer, for new bioplastics to proliferate through the value chain.
Life in bioplastic, it’s fantastic with Hannah Friedman and Keeton Ross’s imagination and creation of this feature. Let’s go party together on the next CTVC plastics installment. What’s your level of interest in a deep dive into the recycling value chain after a recyclable material (like PET, HDPE, paper, glass or aluminum) comes off of the curb? You want to go for a ride? We are just getting started.
Survey results: what’s working, what’s stalled, and what’s missing
A sneak preview from Sightline’s exclusive client-only webinar
Investors hope to set off a chain reaction with new nuclear funding