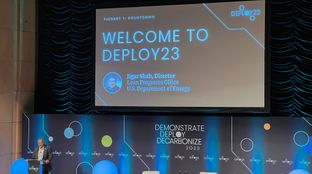
š Demonstrate, deploy, decarbonize with DOE
āGovernment-enabled, private sector-ledā in action in Washington, DC
If the steel industry were a country, it would be the third largest global CO2 emitter - bested only by the US and China. At 11% of all global emissions, decarbonizing this omnipresent industrial material is quite literally foundational to slowing global warming.
Steel has some tricky ratios working against its decarbonization favor - namely, 1 : 1.85. Every ton of steel emits 1.85 tons of carbon dioxide. Fortunately, cleaning up steelās act has been heating up with over 72 low-carbon steel projects, 90%+ of which have been announced since 2019. (Must click: Industry Transitionās green steel tracker). Steel also has some big fresh funding numbers in its favor - namely $3.5B for H2GreenSteelās debt round, $85M for Electraās Series A. Despite being up against fundamental chemistry and massive capital intensity challenges, investors and strategics continue to smelt (okay, pour?) funding into the low-carbon steel startup smithy, in an attempt to extract value (another smelting joke!) from the $1T market opportunity to lower that 1 : 1.85 ratio.
Technically speaking, novel steel decarbonization technologies must overcome two separate challenges:
For the non-forgemen and forgewomen amongst us, there are two steps to make steel. Iron ore is reduced (the oxygen is removed) during the ironmaking process. Then, the carbon concentration is adjusted as it becomes steel in the steelmaking process.
Steelmakers choose between the different industrial routes to minimize their energy inputs (coal, natural gas, electricity) and raw materials costs (iron ore, scrap metal).
Primary Route (BF-BOF): Also called integrated steelmaking, this pathway encompasses raw material processing through final steelmaking. The blast furnace uses coked coal to reduce iron ore to pig iron, which is then transferred into a basic oxygen furnace. Here, oxygen blows over the hot metal to encourage the production of CO2, lowering the carbon content of the final steel produce from 4% to 1%.
Directly Reduced Iron (DRI-EAF): A newer route where iron ore is reduced with natural gas or hydrogen. Small amounts of coal are added in the electric arc furnace (EAF) to provide the carbon required for steel.
Secondary Route (EAF Recycling): Scrap metal is melted via electrodes to produce crude steel. Because this relies on recycled automotive metals containing alloys, the end product is typically lower grade.
New steel decarbonization approaches can broadly be overlaid on the existing steel pathways and broken into three categories: carbon capture, cleaner energy, and alternative pathways.
Capturing emissions from furnaces with point-source methods like post-combustion capture, pre-combustion capture, or oxy-fuel combustion (reference CTVCās previous list of carbon capture innovators here).
These drop-in approaches work with existing steel infrastructure that will remain in operation over the next few decades. CCUS solutions are easily integrated and shared across all kinds of heavy industry. However, the infrastructure doesnāt exist today and these technologies serve as a stopgap. Geographies with less regulation will continue to produce inexpensive steel without CCUS, making this economically infeasible without heavy subsidies.
Decarbonizing the energy inputs of todayās pathways.
Primary Route (BF-BOF):
Innovators: Antora, Rondo, Heaten
DRI (DRI - EAF):
Innovators: Molten, Monolith, C-Zero, Electric Hydrogen, H2Pro, Hgen
Innovators: Terraform Industries, Dimensional Energy, or Electrochaea
There are a few types of furnaces under development for hydrogen reduction:
Notable Projects: H2 Green Steel (see our interview with Chairman Carl-Erik Lagercrantz), MIDREX, GrInHy2.0, Tenova HYL, HYBRIT
Notable Projects: Outokumpu, Posco HYREX, Cincored
Notable Projects: University of Utah
Notable Projects: Voestalpine SuSteel
Though these are well-characterized energy sources that demonstrably work in todayās capital equipment, they need to be cost competitive with conventional energy sources. Further, they need to be scaled to supply the 7% of total energy consumed by steel production.
Despite these solutions above, the silver bullet to steel decarbonization still remains unsolved. As a result, a handful of novel steel production pathways have recently burst onto the scene, from using electricity directly to convert iron ore to steel, shooting lasers, to employing electrochemistry.
Molten Oxide Electrolysis (MOE): Heating iron ore electrolyte to 1600°C via a submerged anode causes oxygen to split from iron, which then can produce high purity iron from low-grade ore. This significantly reduces capital requirements by skipping the upstream stages - thereās no need to produce coke or hydrogen as reductants. The big name here is Boston Metals. Similarly, ArcelorMittal has pioneered the electrowinning process, where a current passes an iron oxide solution causing iron to collect on an electrode.
Aqueous Electrochemical: This process works by dissolving iron ore in an acid and then electroplating it out. This reaction can use low quality iron ore, and runs at room temperature. The notable company here is Electra.
Alternative Heat: These processes use hydrogen purely for the reduction reaction and heat the iron ore with alternative heat sources. Limelight Steel uses light energy to efficiently and rapidly heat iron-oxide, similar to how microwaves are tuned to quickly heat water. Hertha uses a modified electric arc furnace to provide the heat. The potential benefit of this pathway is the ability to electrify and substantially reduce the required energy needed for steelmaking.
Cheap steel wins. Steel is a global commodity with intense international competition for slim margins. Firms compete to take costs out of these major inputs:
Quite literally, thereās no margin for error for novel steel production pathways. New technologies must be meaningfully cheaper on these axes to have a chance at wide-scale adoption.
Beware āCarbon Credit Profitableā. Governments grok the national importance of steel and can enact policies to move the elbow of the marketās invisible hand by incenting clean energy inputs or punishing carbon emissions - influencing which form of steel is the ācheapestā within country borders. Profitability thatās reliant on carbon offsets can ultimately create carbon leakage, where producers in countries with less strict regulations can produce a cheaper dirtier commodity that dominates the market. While CCS has a role to play in the transition, investment should continue to orient for long term insetting by derisking alternative production routes that may prove cheaper - even without additional offset expenditure.
An idle plant rusts. Plants require decades of continuous uptime to pay back the large upfront costs. Downtime for upgrades and installs means less revenue. Therefore, drop-in technologies that can minimize downtime will face smoother adoption. Constant production is essential for new facilities too - where high uptime is needed to amortize the large upfront investment. This makes variable renewables an unlikely component of future steel plants unless we solve long duration energy storage.
Green steel is an energy game. Firms compete on iron ore and energy prices. While thereās some margin in exploring lower grade ore, steelmakers are ultimately betting on their cheapest future source of energy. Whether thatās hydropower in the Northeast for MOE, natural gas in the Permian Basin for methane pyrolysis, or curtailed energy in Australia for a low capex electrochemical process - the future of steel will be forged by the future prices of energy.
Steeling the show! Thanks to Taggart Bonham for forging this feature. When heās not in the smithy, Taggart drops the blacksmith welding apron and dons the vest as a deeptech VC at Playground Global where he focuses on the future of heavy industry.
āGovernment-enabled, private sector-ledā in action in Washington, DC
Well-to-wake pathways to cleaner shipping
Scaling āsymbiotic manufacturingā with Rubi Laboratories